Electric resistance welding (ERW) is a process that has been used for decades to fabricate pipes and other structural components. It is an economical process that combines heat and pressure to join two pieces of metal together, creating a strong bond with excellent corrosion-resistant properties.
ERW pipes are highly sought after in many industries due to their durability, strength, and cost efficiency. In this article we will explore the basics of ERW pipe manufacturing and how it can benefit your operations.
From understanding the fundamentals of the welding process to recognizing its environmental benefits, this guide will help you make informed decisions about using ERW pipes in your projects.
2. Advantages and Disadvantages of ERW Pipes
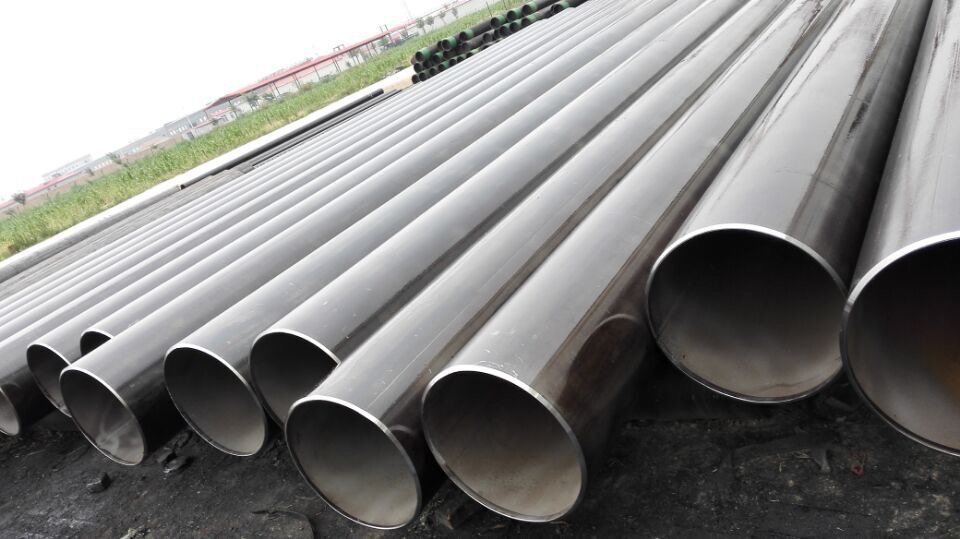
Source: www.nan-steel.com
Electric Resistance Welding (ERW) pipes are a popular choice in the piping industry due to their cost-effectiveness, durability, and versatility. While there are many advantages associated with using ERW pipes, it is important to consider potential disadvantages before making a purchase decision.
The most notable advantage of an ERW pipe is its affordability when compared to other types of welding processes used for piping applications. Additionally, they require relatively simple equipment and can be easily produced in large volumes at short notice which makes them ideal for use in construction projects or other urgent needs.
They also have excellent corrosion resistance properties as well as being resistant to high pressure operations such as oil transport pipelines. However, one major disadvantage of electric resistance welding process is that it produces very few heat-affected zones (HAZ). This could cause problems when welds need to be tested or inspected because HAZ may not be visible enough for accurate assessment without specialized testing techniques like X-ray inspection or ultrasonic examination.
Additionally, the welded joint formed by this method has limited strength and toughness compared with traditional fusion welds which can reduce the overall strength of a structure if these parts are required in structural applications such as bridges or buildings. Finally, the narrow gap between edges where the wires meet during the electric resistance welding process can cause small defects along with incomplete penetration that could lead to an increased risk of failure over time if left unchecked.
3. Benefits of Using ERW Pipe Manufacturing Process

Source: leadrp.net
The Electric Resistance Welding (ERW) Process can provide a number of benefits when it comes to pipe manufacturing. Firstly, the process results in a consistent quality product with high strength properties and minimal defects.
The welding process also reduces labor costs due to its automated nature, allowing for increased efficiency in production as well as significant cost savings. Additionally, the ERW Pipe Manufacturing Process allows for greater control over the welds by using digital controls which help ensure that they are uniform and of strong integrity.
Finally, ERW Pipes offer superior corrosion resistance thanks to their uniformity throughout each weld joint compared to traditional methods such as Longitudinal Submerged Arc Welding (LSAW). Through these various advantages, it is easy to see why more businesses are turning towards ERW pipes for their projects moving forward.
4. Examining the Different Types of ERW Pipes

Source: www.chinhdaisteel.com
In order to understand the electric resistance welding (ERW) process, it is important to look at the different types of ERW pipes available. The most commonly used type of pipe for this purpose is steel-based.
Steel ERW pipes are well-suited for applications that require a high level of strength and durability. Additionally, they can withstand corrosion better than other materials, making them ideal for areas exposed to extreme temperatures or harsh weather conditions.
Other types of ERW pipes include stainless steel and aluminum alloys which offer greater flexibility when it comes to design possibilities as well as improved resistance against environmental factors like saltwater exposure or chemical interaction. Copper-based alloys are also suitable alternatives but tend to be more expensive than their counterparts due to their higher production costs and limited availability in some areas.
No matter what type you choose, understanding how each material interacts with the environment can help you make an informed decision when selecting your ERW pipe solution.
5. Quality Control Measures for Producing ERW Pipes
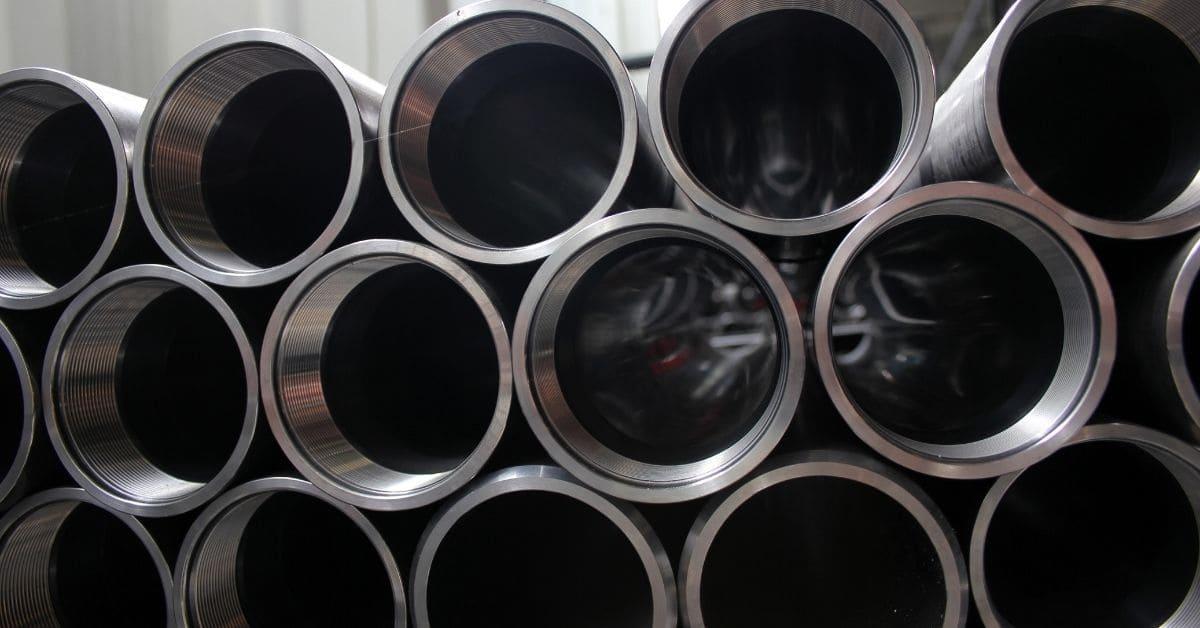
Source: www.stevensec.com
Quality control measures for producing ERW pipes are necessary to ensure that the pipes meet safety and performance standards. Quality must be monitored throughout the entire production process, from raw material sourcing to final product inspection.
To start, suppliers of raw materials should be audited and certified to guarantee quality components for pipe manufacturing. During fabrication, welding operators should adhere strictly to parameters set out in a welding procedure specification (WPS). Regular welder qualification tests should also be conducted to evaluate operator skill levels.
Inspections during and after production can help determine whether welds meet design requirements regarding consistency, tensile strength, wall thickness uniformity, and surface smoothness. Non-destructive testing (NDT) methods like radiography or ultrasonic testing must be applied whenever applicable. As an extra measure of quality assurance, hydrostatic pressure or burst tests may also be used on finished products before delivery if required by the customer’s specifications.
Finally, all records related to inspections and tests performed during ERW pipe production need to be documented as evidence of compliance with industry standards and customer expectations for quality output.
Conclusion

Source: www.pipsisland.com
The Electric Resistance Welding (ERW) process is a highly effective method of producing carbon steel pipes for various industries. This welding process involves passing an electric current through the metal to create heat and pressure, which welds the two pieces together.
The resulting product is a strong, reliable pipe that is able to withstand high levels of stress and strain. ERW Pipes are used in many applications due to their durability and longevity when compared with other types of piping materials such as galvanized steel or plastic pipes.
The use of Carbon Steel Pipe has increased significantly due to its low cost and excellent performance characteristics making it the preferred choice for many applications including water supply lines, irrigation systems, fire protection systems, fuel lines, gas distribution networks and more.