In recent years, the manufacturing industry has undergone a revolution in terms of fabrication technology. One particular innovation that has been a game-changer in tube laser cutting machines.
With their ability to precisely cut and shape complex designs from metal tubes, these machines have enabled manufacturers to create products with greater speed and accuracy than ever before. This article will explore the impact of tube laser cutting machines on modern manufacturing processes, as well as look at some of the new applications being developed for this technology.
In addition, we will discuss how these advances are paving the way for further advancements in both production efficiency and product quality.
Advantages of Using a Tube Laser Cutting Machine
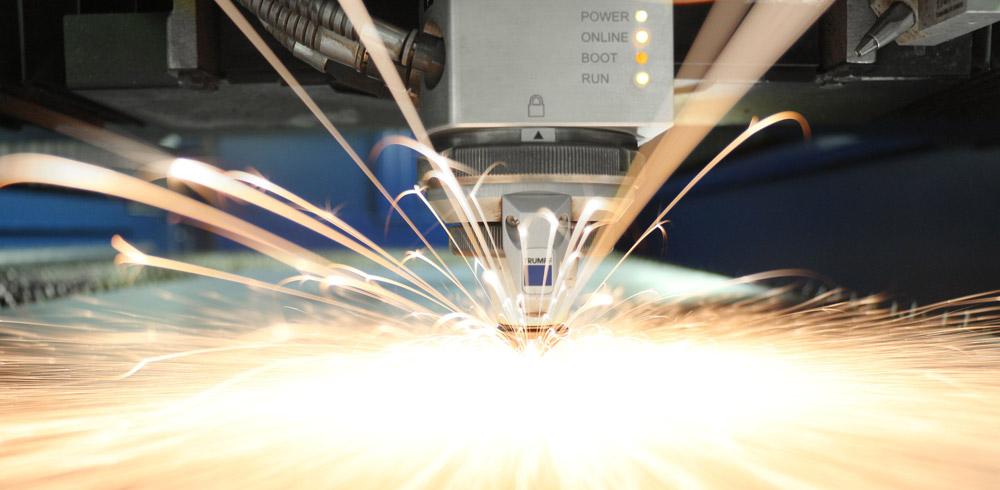
Source: www.thefabricator.com
Tube laser cutting machines have revolutionized the fabrication industry with their ability to offer precise and efficient cutting for a variety of materials. These machines are an incredibly important tool in modern-day manufacturing, thanks to their many advantages over traditional methods.
From increased accuracy and speed to reduced waste, tube laser cutting machines provide a wide range of benefits that keep production costs low and output high. One of the most notable advantages is the improved accuracy provided by these lasers.
By using computer numerical control (CNC) software, fabricators can now program exact measurements into the machine’s system before starting a job; this ensures more consistent results while also reducing time spent on manual measuring tasks. Additionally, because tubes require fewer welds than other material types such as sheet metal or aluminum profiles when cut with a tube laser cutter, there will be less scrap material left behind after each job — further increasing efficiency and decreasing overhead costs.
Another major benefit of using tube laser cutters is their speed; they are much faster than any other type of metal cutting method available today due to their precision-based operation. This means that less time needs to be dedicated to completing jobs which allow for quicker turnarounds between projects as well as shorter lead times for customers\’ orders — resulting in greater customer satisfaction levels overall.
Furthermore, since these machines require minimal maintenance compared to conventional methods like sawing or milling processes there will be lower labor costs associated with upkeep over time too! Overall it\’s clear that using tube laser cutters offers numerous benefits when compared to traditional fabrication methods; from improved accuracy and speed through reduced wastage & labor costs – fabricators across all industries are sure to reap the rewards!
The Impact of Tube Laser Cutting on Fabrication Industries
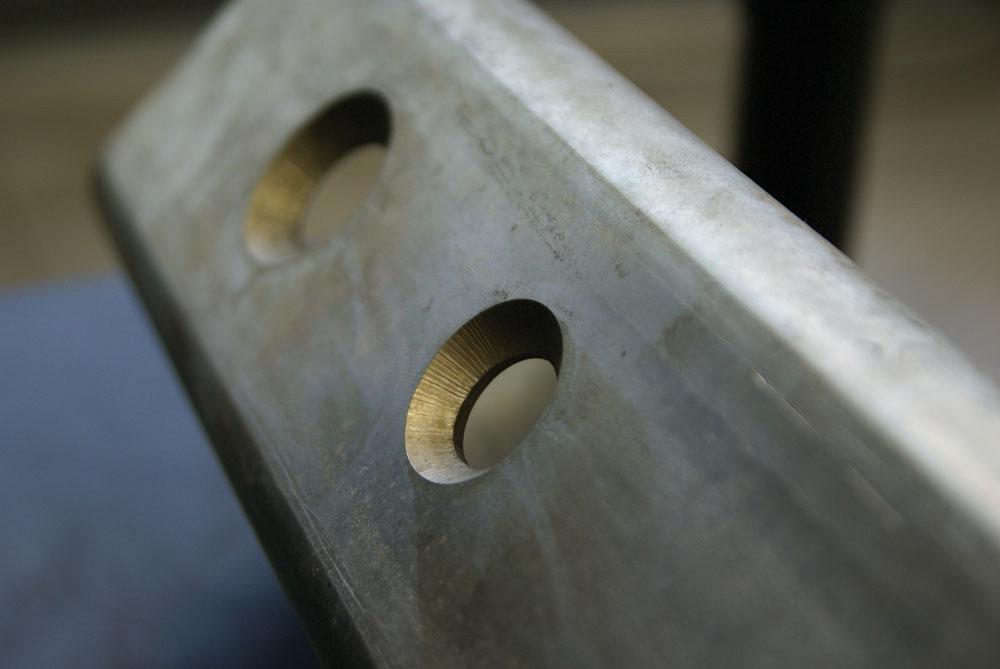
Source: www.canadianmetalworking.com
The impact of tube laser cutting on fabrication industries is undeniable. From the automotive and aerospace sectors to smaller businesses, it has revolutionized how components are produced.
It offers faster speeds, greater accuracy, higher precision, and cost savings compared to traditional methods like plasma cutting or stamping. With its ability to cut complex shapes from a variety of materials quickly and accurately this technology helps manufacturers produce customized parts in less time with fewer errors than ever before.
This has allowed companies to reduce production timescales, cut costs, improve quality control, and increase customer satisfaction levels all at once. As a result of these innovations, many fabrication industries have been able to save significant amounts of money while still providing superior products for their customers.
Tube laser cutting continues to be an integral part of modern manufacturing processes due to its high-performance capabilities making it one of the most sought-after technologies today in the worlds fabrication industries
Innovative Features of Tube Laser Cutters
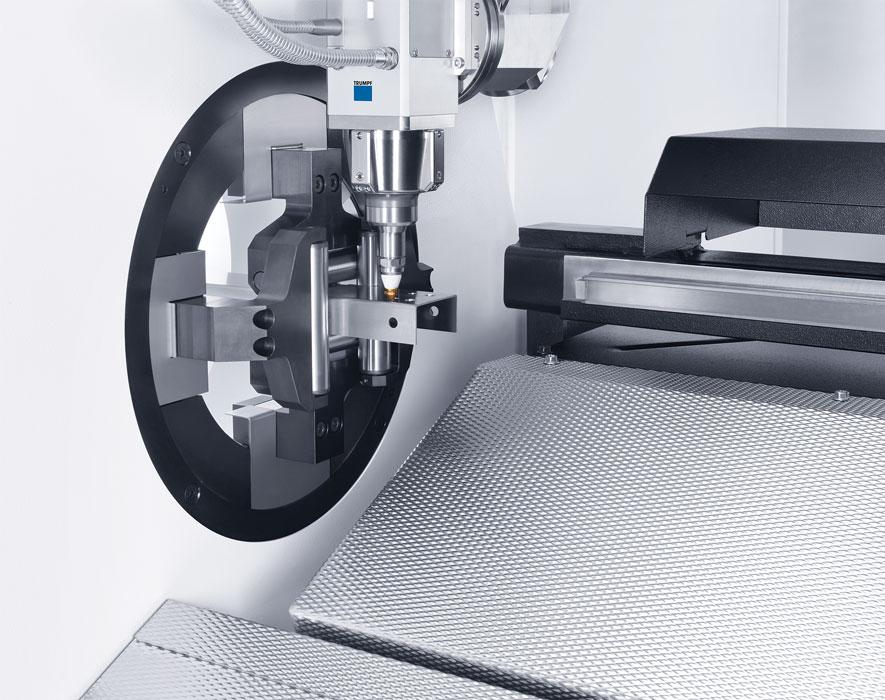
Source: www.thefabricator.com
Tube laser cutting machines are revolutionizing fabrication with their innovative features. These devices can rapidly and accurately cut materials, making production processes more efficient than ever before.
Tube laser cutting machines feature advanced technology that enables them to process intricate shapes, contours, and designs in record time. The high-power laser beam is controlled with a CNC (computer numerical control) machine for precise cuts as well as flexibility in design applications. The speed of tube laser cutting machines allows for quick turnaround times on projects without sacrificing the quality or accuracy of the final product.
With this type of machine, you can create complex geometries with tight tolerances and intricate details without compromising productivity or precision results. In addition, these powerful tools allow for fast prototyping which reduces costs associated with trial-and-error methods used in traditional fabrication processes.
Another benefit of tube laser cutting machines is their wide range of capabilities when it comes to working on different types of materials such as aluminum alloys, stainless steel, copper alloys, and many others – allowing users to customize their finished products according to specific requirements while maintaining consistent quality output each time. Furthermore, there is no need for tooling setup so operators do not need extensive training before using one; they simply program the job into the software interface and press “Go”! The above-mentioned advantages make tube laser cutters an ideal choice for those who want higher levels of efficiency combined with superior accuracy at an affordable cost – revolutionizing fabrication today!
Challenges Faced in Implementing Tube Lasers for Production
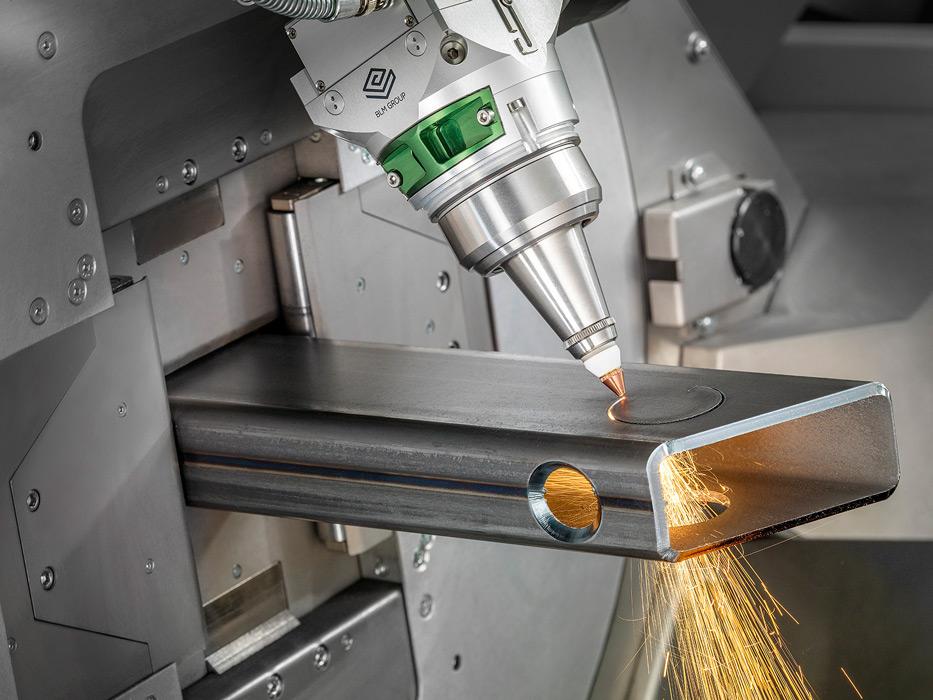
Source: www.thefabricator.com
Despite the many advantages of tube laser cutting machines, their implementation in production can be a challenge. For starters, the cost associated with acquiring and running such a machine is often prohibitive.
Additionally, because these machines are relatively new technology compared to traditional fabricating methods, training staff on them may require additional resources that can further increase costs. Moreover, the complexity of setting up and operating these machines presents another obstacle for organizations contemplating using them as part of their production process.
Furthermore, since tube laser cutting machines operate at high speeds and involve multiple components working together simultaneously, maintenance downtime could have significant operational costs if not managed properly. Finally, it\’s important to consider whether or not there is sufficient space to house such large machinery when implementing tube lasers into production environments.
Emerging Trends and Future Developments in the Field of Tube Technologies
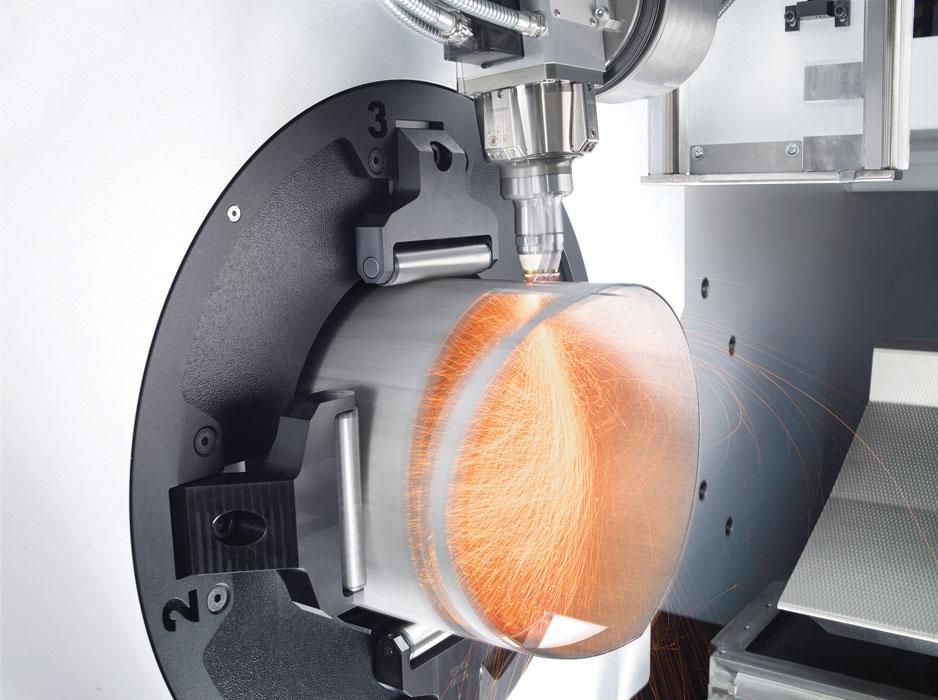
Source: www.thefabricator.com
The field of tube technologies continues to evolve and advance, and with the revolutionizing fabrication abilities of tube laser cutting machines, a new age of potential is on the horizon. In this article, we explore some of the emerging trends and future developments in tube technologies that are poised to shape our world for years to come.
One such development is an increasing focus on automation within tube production processes. Automation can help streamline production processes by reducing or eliminating manual labor, making it easier for companies to meet tight deadlines while still producing high-quality products at cost-effective prices.
Other advances being made include improved accuracy with precision cutting machines as well as increased flexibility when dealing with complex shapes. Another important trend is towards more sustainable practices when working with tubes.
Eco-friendly materials are increasingly being used in both manufacturing processes and final products, allowing for greater environmental stewardship without sacrificing performance or quality standards. Additionally, efforts are being taken towards developing renewable energy sources for use in these operations – further reducing their carbon footprint while helping contribute to a greener future overall.
Finally, an exciting development on the horizon is 3D printing technology specifically designed for use with tubes. This could open up entirely new realms of possibilities when it comes to creating custom designs quickly and easily from any material imaginable – including metals like stainless steel and aluminum! The combination of 3D printing technology plus laser cutting capabilities will enable manufacturers across many industries unprecedented levels of control over their product design process – allowing them to produce superior items faster than ever before thought possible!
Conclusion
Tube Laser Cutting Machines have revolutionized the fabrication industry, allowing for a much faster and more precise way of working. As this technology continues to develop, more businesses are turning to it to improve their production efficiency and quality.
These machines can cut through materials quickly and accurately, without sacrificing precision or accuracy. Furthermore, they can be used for both large-scale projects as well as small ones with great results.
The impact of these revolutionary machines on the fabrication industry is undeniable, bringing about an innovation that enables increased productivity while reducing costs.