Maintaining oil hoses is an essential part of any vehicle or machinery maintenance routine. Without proper upkeep, oil hoses can become a liability for performance and safety due to leaking or reduced efficiency.
Fortunately, with the right knowledge and practices in place, it’s possible to keep your oil hose performing optimally while preventing leakage before it becomes a problem. In this article, we will explore the best practices for maintaining your oil hose and achieving optimal performance and leak prevention.
Pre-Installation Preparation for Oil Hose Maintenance
Pre-installation preparation is an essential part of oil hose maintenance. Properly preparing the hoses and fittings before installation can help prevent leaks and ensure optimal performance. The first step in the pre-installation process involves a thorough inspection to identify any existing damage or wear on the hoses and fittings.
Any damaged components should be replaced before proceeding with the installation. Additionally, it’s important to make sure all fittings are compatible with each other; any mismatch between two components will create a potential leak point which could lead to costly repairs down the line.
After ensuring that all components are compatible, it’s time for lubrication; using proper lubricants on threads will help ensure a tight connection that won’t loosen due to vibration or pressure changes over time. Finally, when connecting multiple sections of the hose, make sure there is adequate slack to allow for movement without stressing the connections too much; this will also help reduce leakage points over time.
Following these steps during pre-installation preparation will go far towards preventing future issues related to oil hose maintenance and extending its lifespan significantly.
Identifying and Replacing Worn or Damaged Hoses
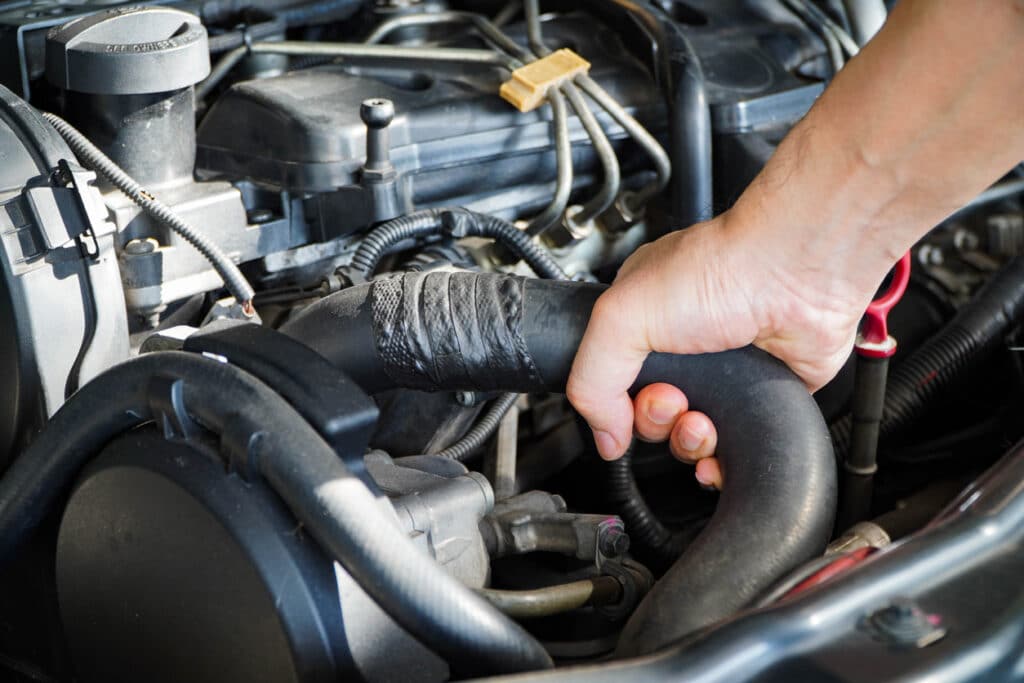
Source: www.holtsauto.com
When it comes to oil hoses, identifying and replacing worn or damaged parts is a key component of maintenance. Worn hoses can cause leakage, which can lead to costly repairs and downtime for vehicles.
In addition, regular inspections are essential for preventing unexpected breakdowns due to wear and tear from everyday use. To ensure optimal performance and prevent leaks, several steps should be taken when inspecting oil hoses: 1.
Visually inspect all hose connections for signs of cracks, wear, or other damage. Replace any hoses with visible damage immediately as this could result in oil loss or leakage if left unchecked.
2. Check the rubber insulation on each hose connection for signs of corrosion or rot – these need to be replaced immediately as they may indicate an existing leak has gone unnoticed until this point.
3. Give each hose a gentle tug test – if there is any movement between the connecting points then replace the entire length of the hose regardless of whether there is visible damage present since looseness will eventually lead to failure over time anyway! 4.
Finally, check all clamps used in securing the connections – make sure they’re not cracked/broken/missing teeth, etc., that their screws are tight but not overly so (otherwise you risk crushing the material) & that they have been correctly adjusted & fitted properly according to manufacturers instructions before re-using them again after inspection & replacement work has been carried out successfully.
By following these simple steps regularly throughout your vehicle’s service life you’ll significantly reduce the chances of experiencing oil pressure issues caused by worn/damaged components such as loose clamps etc., thus ensuring optimal performance & avoiding expensive repair bills down the line!
Regularly Scheduled Inspections and Cleaning Procedures
Conducting regular inspections and cleaning procedures is an essential part of maintaining oil hose systems for optimal performance and leakage prevention. To ensure that the system remains in good working condition, it should be checked regularly to identify any potential issues or wear-and-tear before they become a bigger problem. Additionally, the hoses should be cleaned periodically to remove debris or other contaminants that have accumulated over time.
This maintenance routine will help extend its lifespan and minimize unexpected downtime due to problems related to poor lubrication or contamination. It also reduces the risk of safety hazards by ensuring any leaks are detected quickly so they can be addressed promptly.
Keeping Connectors Secure and Tightly Sealed
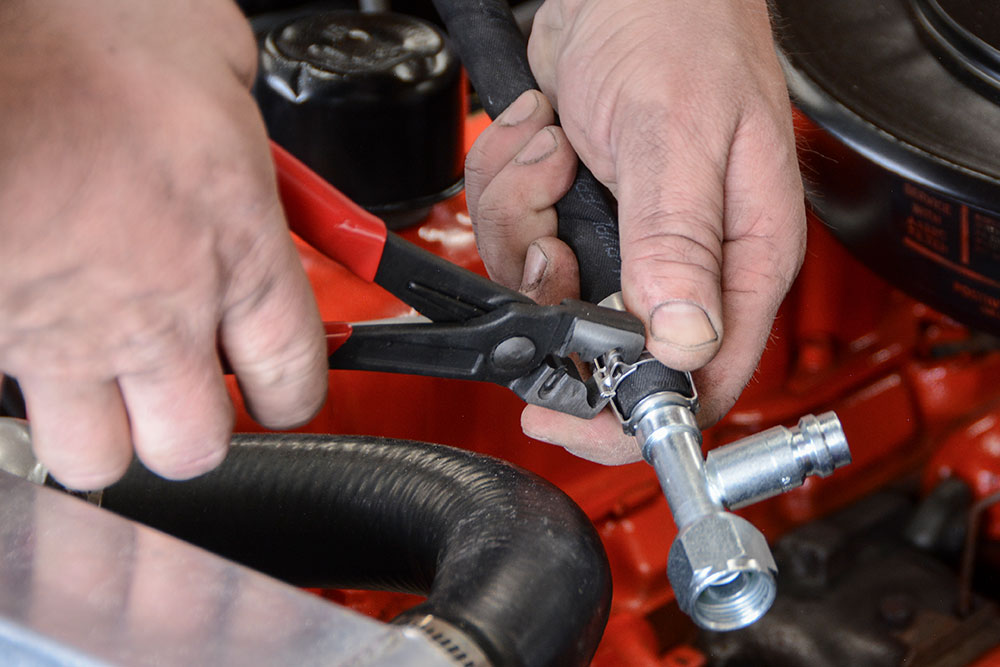
Source: inthegaragemedia.com
Maintaining the security of connectors and keeping them tightly sealed is a key component to extending the life of an oil hose. Poorly secured connectors can result in leaks or other types of damage that will compromise the performance of the hose.
Any user needs to take all necessary steps to ensure their hoses are properly connected, tightened, and secure before use. Proper installation starts with selecting quality parts—connectors should be made from durable materials such as stainless steel or brass, depending on the application requirements.
Avoid using plastic fittings if possible since they may not withstand higher temperatures or pressures over time. Once you have chosen your connectors, make sure to inspect them for any defects or signs of wear before installing them onto your hoses; discoloration or corrosion could indicate a problem with the part itself and should not be used until it has been inspected by a professional technician. Once installed correctly, double-check that each connection is tightened securely but does not overtighten which could cause potential damage to seals and threads within each connector joint.
Additionally, applying thread sealant tape (also known as plumber’s tape) between connections can help prevent leakage through small gaps around threads while also creating additional protection against vibrations which can loosen fasteners over time. Finally, after inspecting all joints visually and ensuring every fitting is tight enough without being overly done so – you’ll know you’ve created safe and reliable connections for optimal performance with minimized risk of leakage!
Conclusion
The maintenance of oil hoses is essential for optimal performance, preventing leakage, and ensuring the longevity of the equipment. It’s important to ensure that proper inspection techniques are used so that any cracks or damage can be identified before they become a safety hazard.
Regular cleaning and lubrication will help reduce wear and tear on the hoses, as well as keep them in good condition over time. By following these best practices for oil hose maintenance, you can rest assured your equipment will run safely and efficiently without issue.